Nagpur Central Railway’s Effective Measures to Reduce Wagon Rejections and Boost Revenue
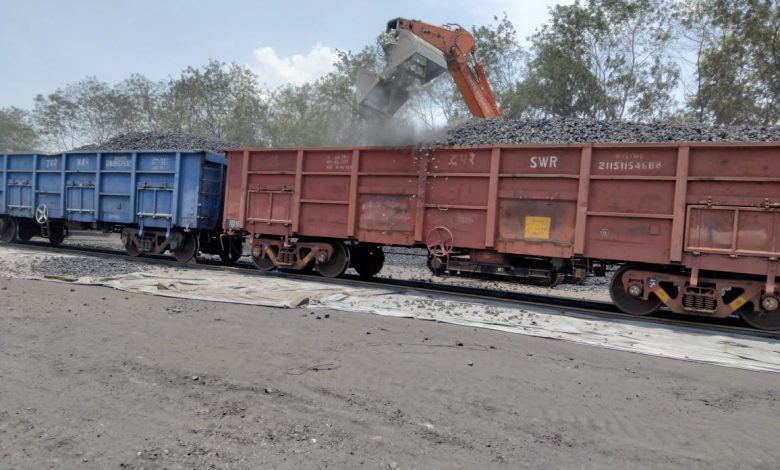
Wagon Rejections Revenue Boost: The Nagpur division of Central Railway has embarked on an impressive journey to tackle wagon rejections, a significant issue causing revenue loss. By addressing the damage to the floor, door, and body of wagons, the division’s mechanical department has made commendable strides. In the fiscal year 2023-24, over 1.55 lakh wagons were reported as unloadable due to these issues. Remarkably, 96% of these wagons were attended to and made fit for loading through in-situ repairs. This initiative generated an additional revenue of Rs986 crore, marking a 33% improvement in wagon attention compared to the previous year.
Wagon Rejections: A Persistent Problem
Understanding the Causes of Wagon Rejections
Wagon rejections occur due to various damages, primarily to the floor, doors, and body. These damages can make wagons unloadable, leading to significant revenue loss and logistical challenges for the railway division.
The Impact on Revenue (Wagon Rejections Revenue Boost)
The financial implications of wagon rejections are substantial. With over 1.55 lakh wagons reported as unloadable in the 2023-24 fiscal year alone, the potential revenue loss was alarming. However, through targeted efforts, the division managed to turn this challenge into an opportunity for revenue enhancement.
Effective Measures Implemented
In-Situ Repairs: A Game Changer
Outsourcing In-Situ Repair Services
The Nagpur division outsourced in-situ repair services at sidings with a high number of unloadable wagons. This strategy ensured prompt and efficient repairs on-site, significantly reducing downtime and improving wagon availability for loading.
Identifying Critical Coal Loading Sidings
Critical coal loading sidings with the highest number of rejected wagons were identified. These included Umred, Makardhokda, Ghugus, Wani, Majri, Chandrapur, and Balharshah. By focusing on these hotspots, the division could streamline its repair efforts and maximize impact.
Stringent Brake Power Certificate Examinations
Targeting High Rejection Rate Depots
Depots responsible for Brake Power Certificate (BPC) examinations of rakes with high rejection rates were targeted. Regular reminders and stringent examination protocols were implemented to ensure compliance and reduce wagon rejections.
Wagon Rejections Revenue Boost: A Tangible Outcome
Revenue Generation through Repair Initiatives
The focused repair initiatives led to a significant revenue boost. The in-situ repair strategy alone contributed an additional Rs986 crore, marking a notable 33% improvement compared to the previous year. This success underscores the effectiveness of the measures taken by the division.
Detailed Look at Key Sidings
Umred Siding
Challenges and Solutions
Umred siding faced frequent wagon rejections due to floor and body damages. By outsourcing repair services, prompt in-situ repairs were carried out, reducing unloadable wagon counts significantly.
Makardhokda Siding
Impact of In-Situ Repairs
At Makardhokda, the introduction of on-site repair services addressed door and body damages efficiently, improving the overall operational efficiency of the siding.
Ghugus Siding
Enhancing Wagon Availability
Ghugus siding, another critical point, saw a marked reduction in wagon rejections due to focused repair efforts. This improvement enhanced wagon availability, supporting higher loading volumes.
Wani and Majri Sidings
Collaborative Repair Efforts
Both Wani and Majri sidings benefited from collaborative repair efforts. By pooling resources and expertise, these sidings saw significant improvements in wagon fitness and reduced rejection rates.
Chandrapur and Balharshah Sidings
Strategic Repair Implementation
Strategic implementation of in-situ repairs at Chandrapur and Balharshah ensured that even minor damages were promptly addressed. This proactive approach minimized wagon rejections and supported consistent revenue generation.
The Role of the Mechanical Department
Proactive Measures
The mechanical department played a crucial role in this success story. By proactively addressing common damage issues and implementing efficient repair protocols, the department ensured the sustained fitness of wagons.
Continuous Monitoring and Improvement
Continuous monitoring of wagon conditions and regular updates to repair strategies ensured that the division could adapt to emerging challenges promptly. This dynamic approach was key to maintaining high standards of wagon fitness.
Collaborative Efforts and Outsourcing
Partnering with Repair Service Providers
Outsourcing repair services to specialized providers brought in expert knowledge and efficient repair techniques. This partnership was instrumental in reducing wagon rejection rates and improving overall operational efficiency.
Leveraging Technology for Better Outcomes
Technological advancements were leveraged to streamline the repair process. Digital monitoring and reporting tools ensured that repairs were carried out efficiently and that all stakeholders were kept informed of progress.
Stringent Compliance and Regular Reminders
Ensuring BPC Examination Compliance
Regular reminders and stringent examination protocols for BPC examinations ensured that wagons met the necessary standards before being cleared for loading. This preventive measure significantly reduced rejection rates.
Training and Development Programs
Training programs for staff involved in wagon examinations and repairs ensured that they were equipped with the latest knowledge and skills. This investment in human resources paid off in the form of higher operational efficiency.
The Nagpur division of Central Railway has set a benchmark with its proactive and efficient measures to reduce wagon rejections. By addressing the root causes of damages and implementing strategic repairs, the division has not only mitigated revenue loss but also boosted overall revenue significantly. The success of these initiatives highlights the importance of continuous improvement, collaboration, and technological integration in achieving operational excellence.
1. What are the main causes of wagon rejections?
Wagon rejections primarily occur due to damages to the floor, doors, and body of the wagons. These damages make the wagons unloadable, leading to operational inefficiencies and revenue loss.
2. How has the Nagpur division addressed wagon rejections?
The Nagpur division has implemented several measures, including outsourcing in-situ repair services, identifying critical coal loading sidings, and ensuring stringent Brake Power Certificate examinations to reduce wagon rejections.
3. What is the significance of in-situ repairs?
In-situ repairs allow for prompt and efficient repairs on-site, reducing downtime and ensuring that wagons are quickly made fit for loading, thereby minimizing revenue loss.
4. How much additional revenue was generated through these initiatives?
The initiatives led to an additional revenue generation of Rs986 crore in the fiscal year 2023-24, marking a 33% improvement in wagon attention compared to the previous year.
5. What role did the mechanical department play in this success?
The mechanical department was instrumental in identifying and addressing common damage issues, implementing efficient repair protocols, and continuously monitoring and improving wagon fitness.